Case one
Successful establishment in Eastern Europe
An industrial equipment manufacturer sought to establish a production unit in Eastern Europe to serve European markets while optimizing production costs.
Case two
Optimization of a production site in Asia
A manufacturing company established in Vietnam faced challenges in productivity, quality, and operational efficiency.
Case Three
Equipment selection for a new European production unit
A European industrialist wanted to diversify production with a new product line requiring specialized equipment, with strict budget constraints.
Successful establishment in Eastern Europe
An industrial equipment manufacturer sought to establish a production unit in Eastern Europe to serve European markets while optimizing production costs.
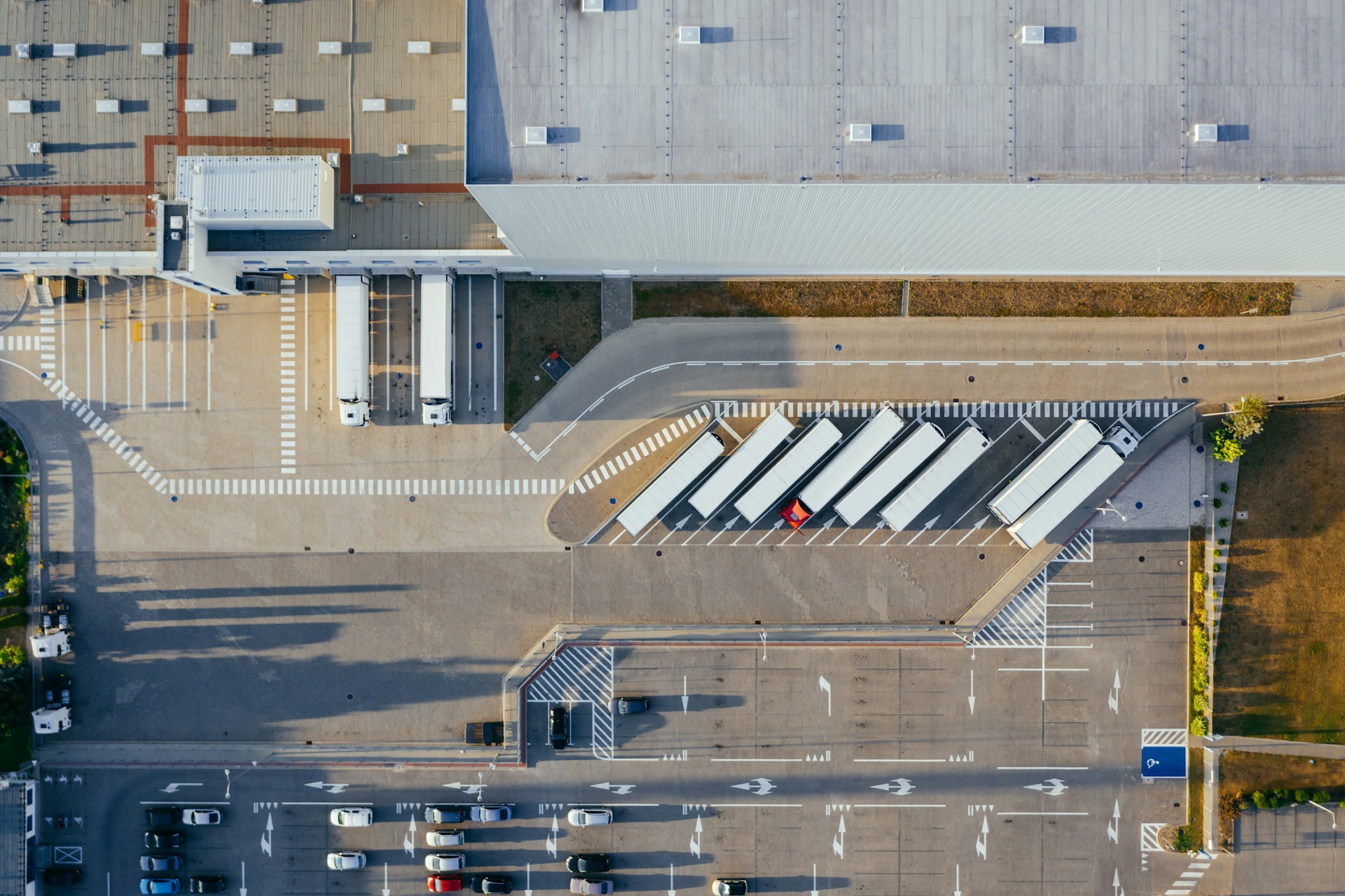
Challenges:
Our approach:
Results:
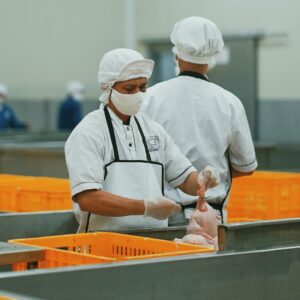
Optimization of a production site in Asia
A manufacturing company established in Vietnam faced challenges in productivity, quality, and operational efficiency.
Challenges:
Our approach:
Results:
Equipment selection for a new European production unit
A European industrialist wanted to diversify production with a new product line requiring specialized equipment, with strict budget constraints.
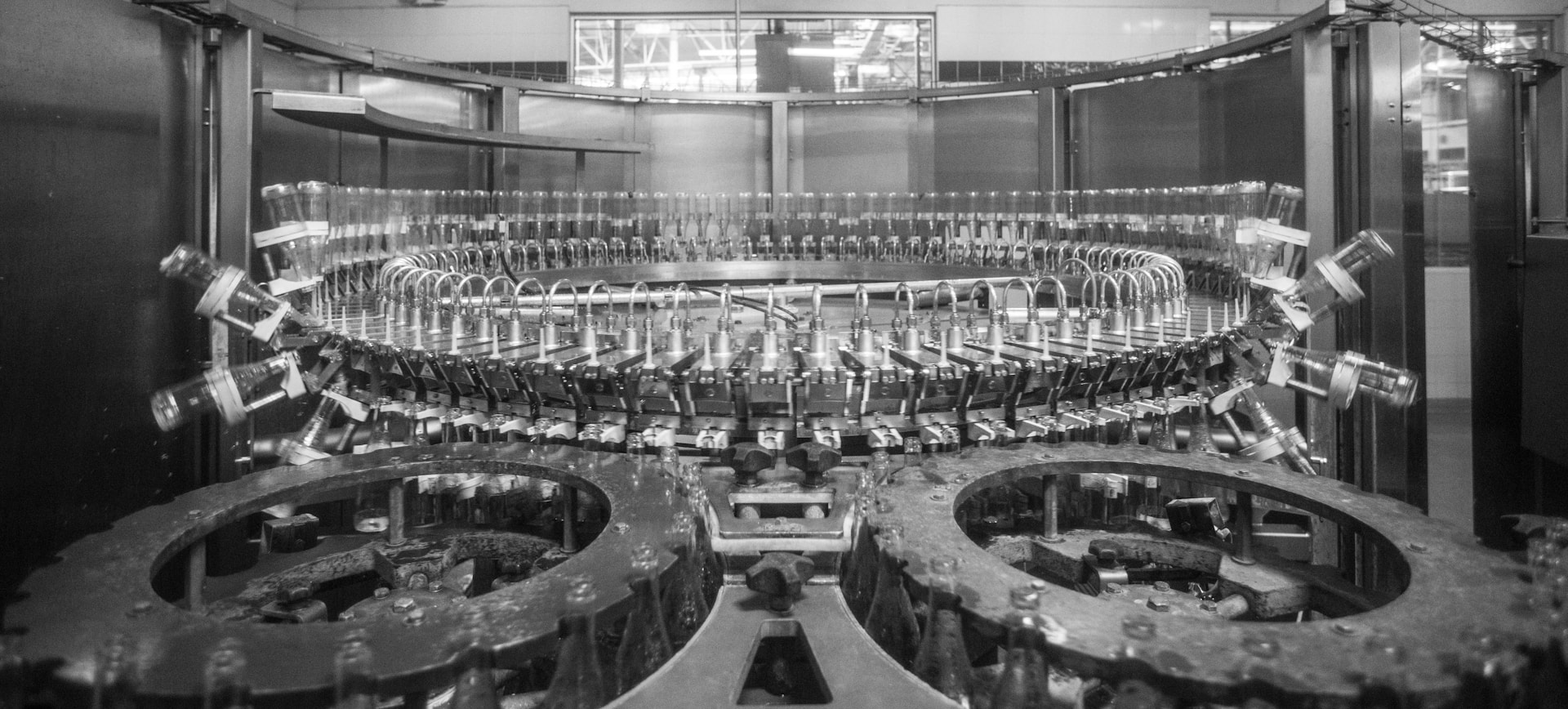